Is Trypsin Inhibitor Exposure being Overlooked?
July 10, 2023
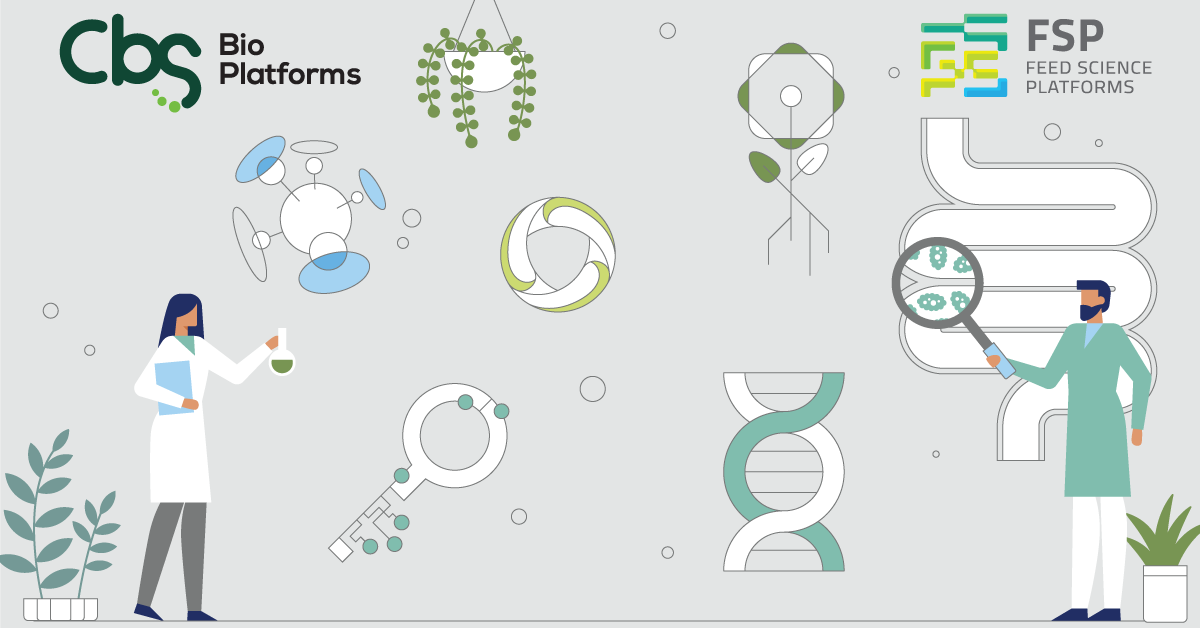
The world is currently experiencing a high cost soybean meal environment, driven by multiple factors including supply-demand disruption due to ongoing transportation congestion, escalating input prices such as fertilizer, as well as supply-demand imbalances due to geopolitical conflicts. Together these factors have pushed soybean meal prices to levels not seen in many years (See Part I). This price pressure has led many feed producers to evaluate the use of non-traditional soybean products such as extruded, cooked pressed full fat soybeans or high fat soybean cakes. However, the use of these alternative protein sources may be inadvertently exposing livestock to anti-nutritional toxins which could be depressing performance and offsetting the savings sought out by using such protein sources.
In Part I of this series, a brief overview of trypsin inhibitors (TI) was provided along with context as to why these anti-nutritional factors should be managed and it was suggested that one key way by which TI can be managed is through continuous monitoring. However, in order to implement such a risk management system, an understanding of the detection methods utilized is necessary.
In practice, there are two basic methods by which laboratories quantitatively measure the presence of TI in feed ingredients. The first and most commonly used method is the ‘Urease Method’. This method doesn’t measure TI directly, but rather relies on the detection of the enzyme urease, a naturally occurring enzyme in soybeans, as a proxy for the presence of TI. The premise being that urease is equally susceptible to heat and processing denaturation as TI, and therefore any urease that survives processing, be it mechanical where the ingredient is ground or pressed or from direct heat exposure due to solvent extraction, cooking, toasting or drying, will be equivalent to the residual content of TI.
The stepwise process of determining urease levels is fairly straightforward. The method begins with grinding soybean meal, or any other feed ingredients suspected of containing TI into a uniform particle size. Following this, the sample is soaked and incubated in a urea-containing reagent. Urease in the sample will react with the urea-containing reagent causing a color reaction. The degree to which the color changes is then correlated to the amount of residual urease which in turn gives an estimate of the TI concentration in the sample.
The second method by which TI are determined is known as the ‘Direct Method’. This method differs from the urease method in that residual TI in the sample of interest are extracted and measured through a colorimetric inhibition assay in order to give a direct quantification of the TI present in the sample. The broad strokes of the direct method include an initial grinding step to ensure homogeneity which is followed with the aforementioned extraction using sodium hydroxide. The extract is then incubated with a reagent containing a color-linked amino acid based substrate as well as trypsin. The trypsin breaks down the substrate inducing a color change that is quantified using a UV spectrophotometer. The reduction in this color change is quantified between the TI containing treatment group and the control, thereby providing an estimate of trypsin inhibition which allows for the determination of TI in the sample of interest. The chart below shows the TI activity of various soy products using the direct method.
As can be seen, there are inherent advantages and disadvantages to each method described above. The urease method for example is relatively inexpensive compared to the direct method and can be run at a commercial lab as well on site at processing facilities that possess basic quality control laboratories. Notwithstanding, as the urease method is a proxy assay, it is susceptible to external interference and decisions made from this procedure should reflect this intrinsic variability. In contrast, the direct method offers the advantage of quantifying residual TI without being prone to external interference. However, the direct method requires the use of more sophisticated instrumentation, as well as purchasing, storing and managing expensive reagents and typically is run by experienced and proficient technicians. These requirements drive up both the implementation and per sample costs of this method and as such is not readily made available at most commercial laboratories. Of course it should be noted that both of these methods only serve to assess under processing and neither provide any information on over processing, the result of which can be heat damaged proteins that have reduced digestibility which in turn can negatively impact livestock performance.
An alternative to relying on third party labs for TI analysis is the use of distributed diagnostic technology, better known as rapid detection kits. There are a number of options available at the moment and for the most part, each kit relies on the fundamentals of the urease method to detect TI. The advantage of using such kits is that samples can be analyzed for TI nearly anywhere with results obtained in hours versus days. Additionally, the cost per sample analyzed is usually substantially less than sending the sample to a commercial lab for analysis. However, rapid detection kits don’t have the same precision nor are they able to detect TI at low levels to the same degree as lab based methods. Additionally, there is a degree of subjectivity that accompanies the use of rapid kits as color change or color formation of the sample is used to estimate TI levels and assessing this color change can vary between the person conducting the sample analysis. Therefore, rapid test kits should be considered a tool or a component of a broader monitoring program that also includes either of the lab based TI analysis methods described above.
The key takeaway is that routine monitoring of TI in alternative soybean ingredients is something any individual or organization that is involved in feed manufacturers should be considering. Whether a monitoring program incorporates either the ureas or direct methods or utilizes distributed diagnostic technology is markedly less important compared to implementation of a program itself, given the impact that TI can have on reducing performance and profitability.